The Vital Function of Tank Welding Evaluation in Ensuring Structural Integrity and Safety Compliance in Industrial Applications
In the realm of industrial applications, storage tank welding evaluation arises as a critical component in safeguarding structural honesty and making sure conformity with safety laws. Using a combination of methods such as aesthetic analyses and advanced screening techniques, these assessments serve to identify and minimize prospective defects before they rise into significant threats. The ramifications of these practices expand past mere governing adherence; they essentially impact functional effectiveness and asset durability. Nevertheless, the complexities bordering the evaluation procedure trigger a closer examination of its methods and outcomes, exposing layers of importance that merit additional exploration.
Relevance of Tank Welding Evaluation
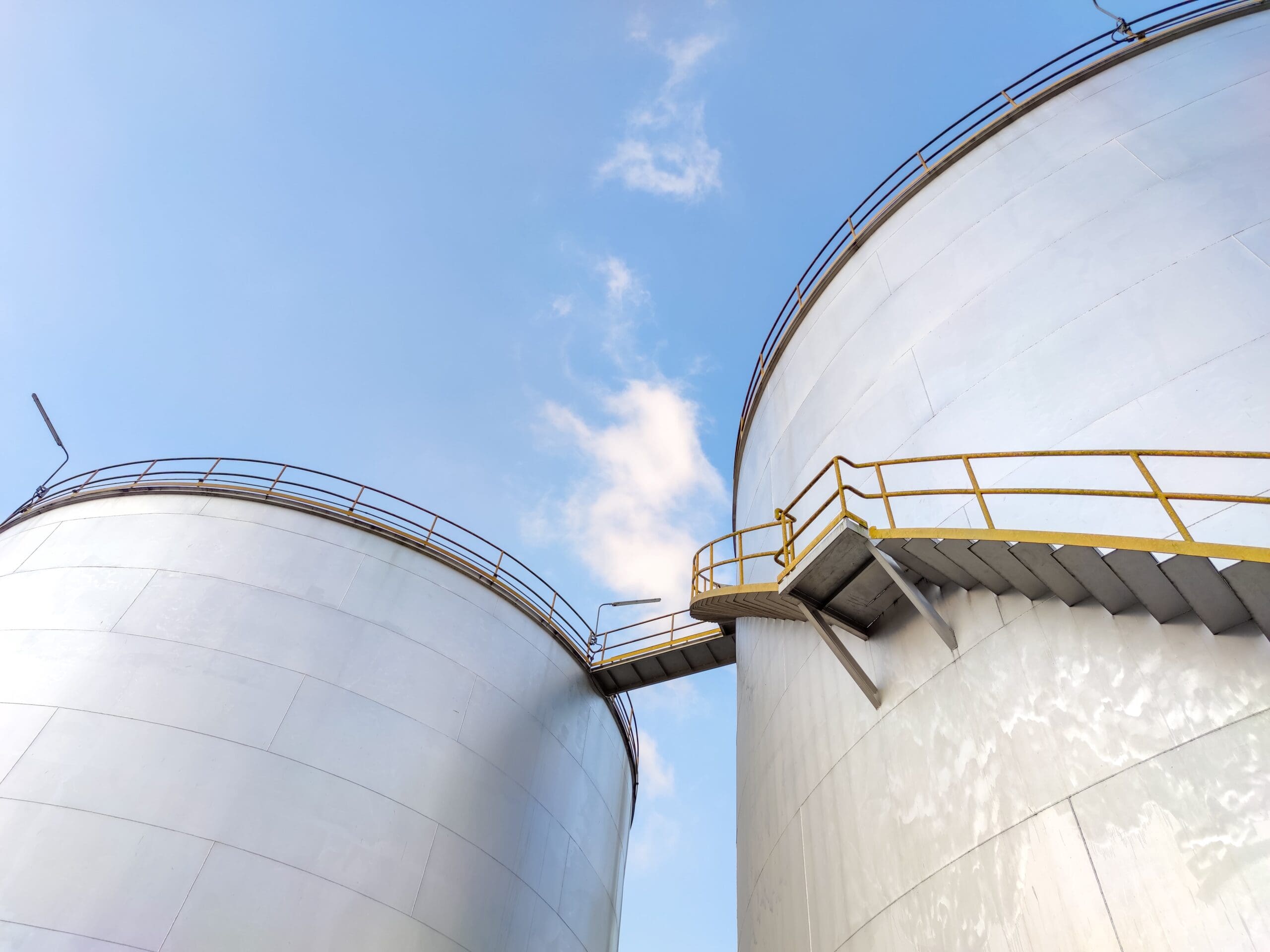
Ensuring conformity with sector criteria and laws is another considerable element of container welding assessment. Governing bodies mandate stringent standards for the building and construction and upkeep of tank, and thorough evaluations assist organizations follow these demands. Non-compliance can lead to serious penalties, consisting of penalties and shutdowns, better stressing the demand for strenuous assessment procedures.
Additionally, storage tank welding evaluation plays a critical function in preserving operational efficiency. Regular analyses can recognize prospective problems before they escalate, assisting in timely fixings and lessening downtime. This positive method not just boosts security but also adds to cost financial savings in the lengthy run. In summary, the relevance of container welding evaluation lies in its capacity to secure public wellness, safeguard the setting, and make sure compliance with governing structures.
Secret Examination Techniques
Effective tank welding assessment relies on a range of vital techniques that make sure thorough assessment of weld high quality and structural integrity. Among one of the most prevalent methods are aesthetic examination, ultrasonic testing, radiographic testing, and magnetic particle testing - Tank Welding Inspection. Each technique provides special benefits in assessing different elements of the weld
Aesthetic assessment works as the very first line of defense, enabling assessors to recognize surface defects, irregularities, or variances in the weld grain. Ultrasonic screening uses high-frequency acoustic waves to discover interior problems, such as splits or gaps, giving a comprehensive assessment of weld integrity. This method is specifically reliable in finding concerns that might not show up on the surface area.
Radiographic testing uses X-rays or gamma rays to produce photos of the welds, exposing inner gaps and providing a permanent record for future referral. This method is extremely reliable for crucial applications where the risk of failure need to be lessened.
Last but not least, magnetic fragment testing is utilized to recognize surface area and near-surface flaws in ferromagnetic materials. By applying magnetic fields and great iron fragments, examiners can identify discontinuities that might compromise the architectural stability of the tank. With each other, these strategies develop a robust structure for making certain premium welds in commercial applications.
Conformity With Safety Standards
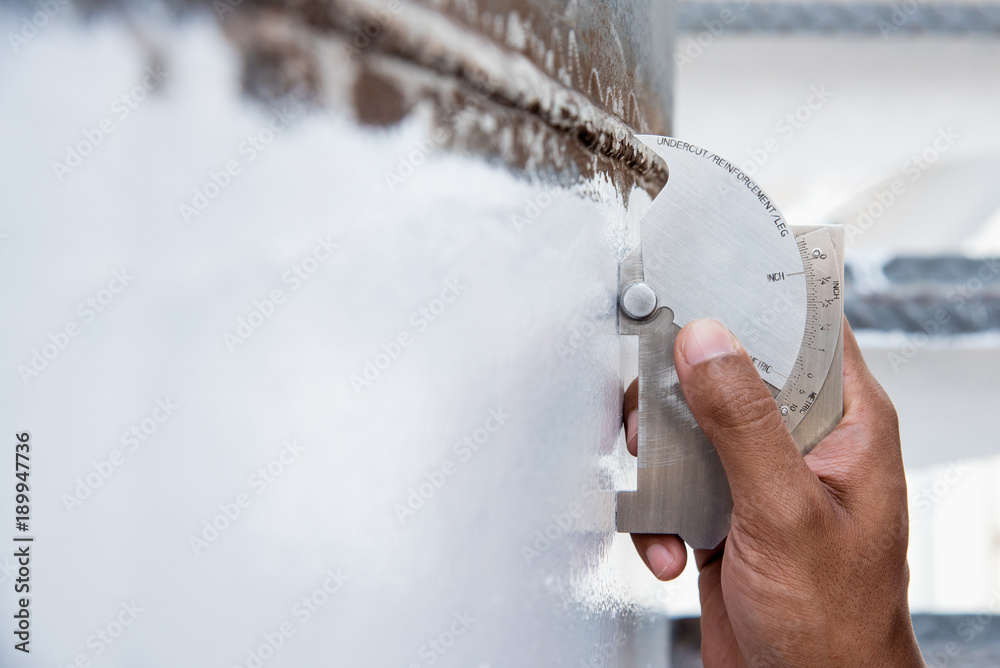
Normal inspections play a critical duty in guaranteeing conformity by determining potential failures or deviations from recommended standards. Inspectors are trained to review weld quality, validate material specs, and assess the general structural integrity of storage tanks. Their know-how is important in guaranteeing that welding processes meet the needed safety and security criteria.
In addition, compliance with safety criteria not only protects employees but likewise safeguards the setting from potential risks such as leakages or devastating failures. Organizations that focus on safety and security conformity are much better positioned to mitigate risks, improve operational efficiency, and cultivate a culture of security within their labor force. In recap, keeping rigorous compliance with security criteria is indispensable for the successful operation of container welding tasks in industrial settings.
Benefits of Routine Assessments
Normal examinations are integral to preserving the structural honesty and security of bonded tanks. These inspections supply an organized approach to identifying potential defects or weaknesses in the welds, making certain that any kind of problems are dealt with before they intensify into considerable failures. By carrying out normal assessments, companies can detect rust, tiredness, and various other types of degeneration that may jeopardize tank performance.
Additionally, regular assessments contribute to conformity with industry regulations and standards. Adhering to these standards not just alleviates legal dangers but also boosts the company's track record for security and reliability. Regular examinations cultivate a proactive security culture, urging staff members to acknowledge and prioritize the relevance of devices stability.

Study and Real-World Applications
Case research studies and real-world applications highlight the tangible effect of reliable tank welding evaluation techniques. Complying with the implementation of strenuous welding inspection protocols, consisting of aesthetic and ultrasonic click this site screening, the facility identified important imperfections in weld seams that might have led to disastrous failures.
Similarly, a water treatment plant carried out a thorough inspection program for its tank welding operations - Tank Welding Inspection. By integrating non-destructive screening approaches, the plant had the ability to detect very early signs of deterioration and exhaustion in weld joints. This timely intervention extended the lifespan of the tanks and guaranteed compliance with safety and security guidelines, hence guarding public wellness
These instance researches emphasize the relevance of normal and methodical container welding assessments. By focusing on these methods, markets can mitigate threats, boost structural honesty, and ensure conformity with security standards, inevitably bring about improved functional performance and minimized obligations.

Final Thought
In verdict, tank welding assessment is an essential part of maintaining architectural integrity and security in commercial applications. Using different examination methods ensures early discovery of potential problems, therefore stopping tragic failings.